According to The Robot Report published in 2016, China accounts for 30% of the world’s robotics equipment in the industrial sector. And this number is poised to increase further over the next few years to 40% of global supply. In the solar industry recently, Chinese companies have acquired a handful of major European robotics companies. One of the most high profile examples in recent years was Midea’s purchase of the German robotics firms Kuka.
Midea is among the top three robotics companies in China, and has been immensely strengthened by this acquisition. Other notable maneuvers by Chinese robotics firms into Europe include ChemChina’s purchase of KraussMaffei from Munich, Germany.
Moreover, presently some 800+ robotics companies are operating across China.
Wilmer Zhou, Senior Analyst, Manufacturing Technology Department of IHS Markit in China told pv magazine that the leading robotics names in the solar industry are now nearly all Chinese-owned: Siasun, GSK, Estun, Step, and Kuka.
This apparent push to ramp up automation in China’s leading industries stems from a directive from President Xi Jinping’s Made in China 2025 program, which calls for a “robot revolution.” The idea behind this program is to reboot, modernize, and future-proof the Chinese manufacturing sector. And as the Industry 4.0 revolution whirs into gear, all industries are going to become more automated – with solar in prime position to lead where others follow.
Tongwei tells all
Last September, Anhui, China-based cell and module manufacturer Tongwei unveiled its new production line, which it is calling the world’s first ‘Industry 4.0’ ready line. The project adopts intelligent online automatic production equipment and comprises the first all-in-one unstaffed production line in China.
The primary function that the production line will serve is to realize the smart production process, which Tongwei believes will substantially increase production efficiency and reduce the cost of manual labor, particularly among production operators.
The production line is expected to produce 1.35 million efficient batteries a day. Over the next three years, Tongwei’s solar cell manufacturing division plans to reach a total of 10 GW capacity. To be able to reach this target – and to do so competitively in a space that is intensely fierce – the company is planning to build robotics-driven intelligence directly into its new fab lines.
Semi or fully automated?
A great number of solar companies proudly state that they have fully automated production lines, but the question often remains: How fully automated are they really? And why does it matter?
IHS Markit’s Zhou has addressed such questions many times before. Zhou says, “It is not possible, and not necessary, to have a ‘fully automated line’ in the solar industry.” It is far easier – and makes more economical sense – Zhou adds, to employ a reduced manual workforce dependent on the types of operation being carried out. Furthermore, he stresses, some level of manual intervention or supervision will be required eventually, particularly in the event of machine fault or breakdown.
Zhou explains that industrial robots are going to penetrate into all PV manufacturing sectors rapidly throughout China over the next two years. Primarily, robots will initially be found in the workstations of material handling, dispatch, feeding, loading and unloading, welding, coating, deposition, assembly, and much more. However, manual labor will still be a vital component in the production sectors of electronics assembly, and for some packaging duties.
“There is no real fully automated line in China,” Zhou says. He explains that the level of difficulty for automated solutions in mass industry is as follows: Automotive > semiconductors > flat panel display > automatic warehouse > electronics > solar > LED equipment.
A question of quality
As solar demand accelerates, so too does the expectation of quality and increased output. Upon these two pillars, robotics can certainly prove valuable. Hence, all new manufacturing facilities or production upgrades in China are automated.
However, the question of whether going towards full automation makes economic sense from a capex perspective persists in many countries, particularly those where quality concerns remain secondary and labor is generally cheap. But looked at from another perspective, the growth of Industry 4.0 is creating more jobs in IT and computing, with a greater focus on skilled employment that ensures the smooth operation of the line through real-time, online communication and computational analysis.
This extra thread adds to what has become a near endless debate, but a vital one nonetheless, because robotics is no longer a fancy futuristic word, but a contemporary necessity. The need for ensuring the stability and consistency of the production process, reducing losses and waste, increasing capacity and energy utilization, delivering faster and repeatable analysis, and producing with precise parameters, is growing all the time.
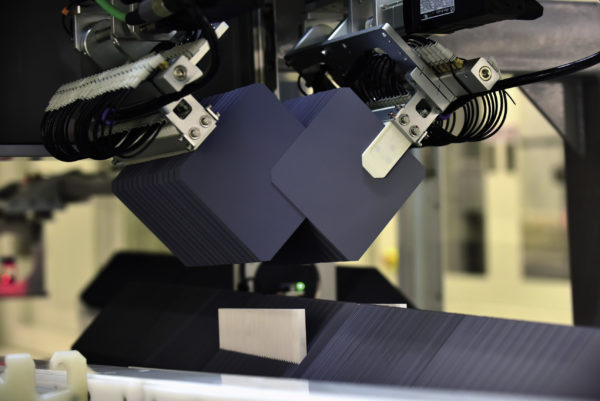
Automation has many tangible targets in sight. Storage, for example, is still expensive, and battery costs need to be reduced in order to help drive the anticipated revolution in the energy mix.
And for battery components to become cheaper, improved manufacturing lines with a highly efficient production process are a must. Reaching this goal is a task made much more reachable with automation.
Cheap labor against automation
Despite cheap labor in India and China, these nations are nevertheless taking great strides towards automation. However, it is still common to see some module manufacturing facilities reliant on manual labor, while nearly fully automated lines are usually the reserve of the larger firms. Zhou says, “The automation implementation depends on the price-performance ratio – the employer will calculate the return on investment (ROI).”
According to The Robot Report, India enjoyed 14% growth in industrial robotics shipments between 2016 and 2017. Commenting on the automation scenario in India’s solar sector, Dharmendra Kumar, analyst, solar energy department of IHS Markit, India says, “Indian solar manufacturing is still dependent on manual labor, and moreover much of the equipment that is being used currently is also outdated.”
Kumar does confirm, however, that Adani Group is looking at procuring automation equipment for its PV fab. “But they are still in the planning phase,” he says.
In-house or outsource?
China’s robotics industry is growing in lockstep with its PV sector. Even so, the major high-end robotics are largely sourced from overseas. This is where Japanese and European robotics suppliers dominate over 70% market share, Zhou says.
Japanese companies, for example, are dominant in the robotics supply market for China’s battery industry. Leading Japanese robotics companies for this sector are Yaskawa, Fanuc, Mitsubishi, Denso, and Daihen. From Europe, ABB enjoys good penetration into both solar and storage in China, Zhou outlines.
This content is protected by copyright and may not be reused. If you want to cooperate with us and would like to reuse some of our content, please contact: editors@pv-magazine.com.
By submitting this form you agree to pv magazine using your data for the purposes of publishing your comment.
Your personal data will only be disclosed or otherwise transmitted to third parties for the purposes of spam filtering or if this is necessary for technical maintenance of the website. Any other transfer to third parties will not take place unless this is justified on the basis of applicable data protection regulations or if pv magazine is legally obliged to do so.
You may revoke this consent at any time with effect for the future, in which case your personal data will be deleted immediately. Otherwise, your data will be deleted if pv magazine has processed your request or the purpose of data storage is fulfilled.
Further information on data privacy can be found in our Data Protection Policy.