The lamination step known as encapsulation is, in broad terms, similar to a visa application: At the time of submission, all documents must be present and correct and in an orderly fashion, lest problems arise. If everything is in its right place, the application will be accepted and then formalities can proceed. Similarly in module production, before approaching the lamination phase all of the module components should be laid up neatly and in the correct order as per the appropriate design of the solar module. After the lamination process, all that is left are the framing, checking, and measuring steps, and the job is done.
A solar module is a composition of several components, which are thermally treated in the production process chamber under vacuum, pressure, and temperature parameters. The lamination step bonds all of these materials together to form a single fabricated module. Encapsulants like ethylene vinyl acetate (EVA) or polyolefin (PO) are used in the bonding process, which makes this production step one of the most critical along the module manufacturing line, depending on the module type. The process know-how of ensuring that the correct parameters are employed ultimately determines the end quality of the product.
Therefore, it is the responsibility of the equipment supplier to build and deliver quality machines, and a laminator to professionally produce defect-free modules. Currently, several companies operate in this market. The primary laminator providers are: Jinchen Machinery Co. Ltd., Boost Solar Photovoltaic Equipment Co. Ltd., Zenithsolar Technological Co. Ltd., and Yiheng Science & Technology Co. Ltd. from China; NPC Inc. and Nisshinbo Mechatronics Inc. from Japan; Meyer Burger Technology AG from Switzerland; Robert Bürkle GmbH from Germany; Teknisolar Ltd. from the U.K.; and Ecoprogetti SRL from Italy.
Glass-glass lamination complexity
According to the International Technology Roadmap for Photovoltaic (ITRPV) Eighth Edition 2017, glass-glass (GG) modules will claim around 37% market share by 2027. These GG modules have several advantages over glass backsheet (GB) modules, although their production is not quite as straightforward as that for the latter type.
The preparation and lamination process for GG modules requires twice the parameters needed to control a two-step process. If these parameters are overlooked, then the process time will be doubled. There are, however, already several improvements on the market where the production of defect-free GG module lamination is evident.
For lamination, the first level process was incorporated with the active lifting pins installed on to the heating plate, promoted first by Bürkle, Meyer Burger, and Wemhöner GmbH & Co. KG. Now, almost all Chinese laminators have this feature. The pins work by taking the module up and down, according to the process. This prevents the module from coming into direct contact with the heating plate during the no pressure intermediate cycles that are part of the process. Thus, they help to ensure a homogeneous heat transfer onto the module. Pins are also used for GB module production.
Bürkle has designed two-side heating processes for a second step, which helps to transfer the heat into the modules much more quickly than single-side heating, and thus hastens the process time. Such design innovations have also been implemented in Meyer Burger and Teknisolar machines.
However, if the machine supplier or even the solar manufacturer does not possess the requisite understanding of how materials behave with respect to temperature, time, and pressure, then no matter how advanced the machine is it cannot produce a good quality module. The industry is aware that GG lamination suffers several defects due to such incorrect processes. Apart from the typical defects like bubbles and voids, the module can also suffer encapsulant squeeze-out, and glass shifting. EVA or PO squeeze-out leads to further defects like cell shifting, and voids on the edges and corners. If the pressure is too high, then there is a chance of cell breakage and even glass damage.
There are several ways to avoid such defects. Chinese laminator suppliers laminate their GG modules using the frame to support the module from all sides, which helps prevent glass sliding, breakage at the corner, and encapsulant squeeze-out.
However, the inclusion of such frames creates additional work and non-value added (NVA) operations in the cycle time. Therefore, Bürkle has developed a technology that does not need an additional frame and shows no edge pinching in the GG module. The German firm presented this technology last year at the 33rd EUPVSEC conference held in September in Amsterdam. Bürkle has reached an edge thickness deviation in the GG module ranging from 0.05–0.4 mm, which is an excellent value, according to researchers at École Polytechnique Fédérale de Lausanne.
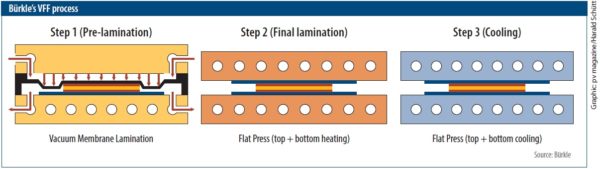
Increasing output per footprint
Bürkle is one of Europe’s most prominent laminator suppliers. Based in the southern part of Germany, the company is forging a reputation for its patented multi-stack three step lamination machine. The basic one stack (or level), three-step laminator is called the Easy-Lam VFF (vacuum-flat-flat), which means that the first step of its process is to evacuate all the air and impurities, and create a vacuum in the membrane press. The following second and third steps handle the curing and cooling process respectively. The company’s Ypsator VFF incorporates this technology into a multi-stack machine to increase the production capacity and thus saves on space. Bürkle has developed its Ypsator up to seven levels, providing 180 – 250 MW annual capacity, which sets it apart from other laminator manufacturers in terms of capacity in a single machine.
Bürkle developed this technology in 2006. However, for the last two years, competitors from China have been exploring ways to design a similar machine. Currently, as per market figures, Boost Solar has a two-level laminator introduced in 2017 called the Double-Deck Double-Chamber (BSL2436DD01), while Jinchen has also built a new model of its laminator, which is defined as the JC LAM double-layer three chamber laminator. However, the most ambitious player is Yiheng, which has developed a two-stack laminator with different combinations, as well as a three-stack triple stage laminator that has reached an output of 200 MW per annum.
Vikas Singh, Sales Manager International at Jinchen, tells pv magazine that the new laminator launched this year is available in two variants: the JCCY2446-DST-C, with a capacity of 130 MW a year, and the JCCY2456-DST-C, with a capacity of 160 MW a year. “This means that for the same footprint you can double your capacity,” he says. “We have recently installed 15 of these laminators in China’s domestic market.”
Not to be outdone, Bürkle has also presented a faster lamination process for both GB and GG modules using EVA encapsulants, reaching a lamination speed that shaves 20% off the conventional 7-8 minutes, according to the research paper published during EUPVSEC.
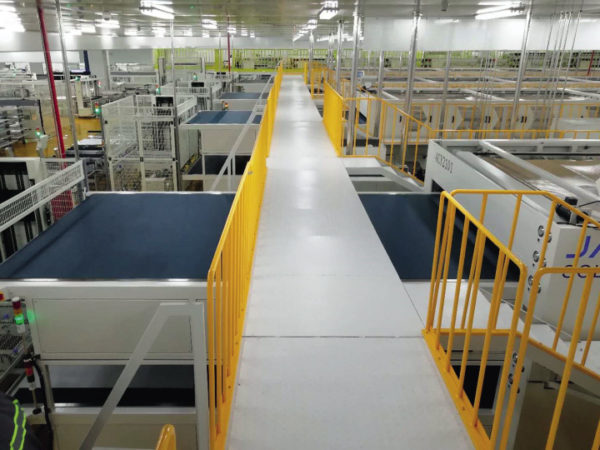
Who’s leading from China
Interestingly, of the prominent laminator manufacturers in China, the majority are clustered around the Qinhuangdao region. Boost Solar, Chongjing Technology Co. Ltd, Zenithsolar, Yiheng, and Radiant Automation Equipment Co. Ltd are all from that area of the country. Only Jinchen is located elsewhere, in Yingkou.
According to ENF Business Consulting (Wuhu) Co. Ltd. (ENF Solar), a global solar directory, of the aforementioned firms it is Jinchen that has the highest number of staff, with 800 employees. Boost and Yiheng have 500 and 400 employees respectively. These numbers represent the entire workforce for whole segments of the factory.
Such statistics show Jinchen’s strength domestically, and the potential it has to continue its global expansion. “In the next three months our order book is full, and we are delivering 6.7 GW of machines in the domestic and international markets,” Singh confirms.
Jinchen has four manufacturing units and one R&D center in China. Foreseeing strong demand, Jinchen has opened an additional sales office in Suzhou city (Jiangsu province). Singh also reveals to pv magazine what new features the company’s latest laminator machine boasts.
“There are two layers, which have an independent circulation system for each, and can operate independently. One chamber does not affect the normal operation of the other chamber,” he says, adding that the cooling system also has an interesting feature. “Configuration of the cold-press system is uniform, with rapid cooling of components, an increased EVA transmittance of components, and an ability to void sheet wrapping, making it easy to cut and test the process.”
Placing Bürkle’s Ypsator VFF in the league of multi-level laminators has helped its global sales. Robert Gaiser, the newly appointed Sales Manager for PV at Bürkle, tells pv magazine that around 700 MW has been sold to companies covering the U.S. and Chinese markets. A further 1,000 MW of Easy-Lam VFF machines have been sold to companies located in Italy, China, and Turkey, Gaiser confirms. Interestingly, all of these machines are procured for almost all kinds of technology, from crystalline modules (mono, poly, n-type, p-type, bifacial, half-cell) to thin film (CIGS, CdTe). “As well as new innovative BIPV module designs, most will be based on GG module designs, which the VFF process is especially developed for,” adds Gaiser, who also reveals that the two lab machines have been sold to research institutes in Germany and Singapore.
Realizing the fierce competition from the Chinese market, Daniel Klaus, who handles R&D for PV at Bürkle, tells pv magazine, “In the past two years we have tested all kinds of combinations of components: cell type, encapsulant types including EVA, PO, different backsheet types, double glass. This has helped us to enrich our process know-how and bring flexibility to the machine.”
One Bürkle client from China was on-site when pv magazine visited, conducting tests for their new CIGS thin film module. pv magazine was invited to witness the lamination process of the module, and an official from the Chinese firm revealed, “Bürkle has an adequate R&D facility, and with its experience, we are able to conduct the development in the lamination process for our CIGS technology. This helps us to save time and cost, and gives us more confidence before going into production.”
To expand into China, Bürkle opened a subsidiary in China. Ken Song, Sales Head for Photovoltaics at Bürkle Machinery Shanghai (BMS), told pv magazine during the REI Expo 2018 India in September, “Our machines bring energy savings, less footprint, less requirement of automation units, higher production, and lower maintenance. With all this quality, the TCO will be lower in comparison to cheap laminators from China.”
Bürkle is on course to deliver approximately 1.8 GW of laminators by the end of 2018, including 506 MW for thin film production. The company is aware that it has a tough battle ahead, however, as Chinese companies like Yiheng, Jinchen, and Boost Solar are developing their own laminators and have begun selling two-level laminators into the domestic Chinese market, on a similar idea of production line optimization.
No membrane laminator
There are very few companies that have a laminator with no membrane. Mostly, companies that deliver the one-step process use a membrane, and almost all of the Chinese laminators also use a membrane in the second and third steps of the three-step (or three-stage) lamination process. Therefore, companies chiefly from Europe, such as Meyer Burger and Teknisolar, have built such machines. Surprisingly, Meyer Burger is no longer a player in this lamination journey. The Swiss PV equipment giant announced last November that its “JT laminator Technology will be discontinued.”
Hence, only the U.K.’s Teknisolar continues to promote this technology in Europe. The company calls its membrane-less multi-stage laminator the Robostak Gen. V. Normally, membrane (either silicon membrane, or Lamibran with a special covering on the silicon layer) is one of the consumables in the laminator process, and hence covered under operation costs, depending on its lifetime. Moreover, at the end of the membrane lifetime, if it is not monitored and replaced in a timely fashion, it can break during the cycle and result in an unfinished module and production loss. Thus, Teknisolar has confirmed that if there is no membrane, then such issues – along with inherent GG lamination problems – could be avoided.
Teknisolar claims that it can produce 60 modules per hour, reaching a maximum capacity of up to 160 MW a year. Another difference that sets the firm apart is its use of electrical heating, which is in contrast to Bürkle and emerging Chinese laminators, which use oil heating.
Teknisolar’s Robostak datasheet mentions how the multi-stage machine has a process time of three minutes for standard crystalline modules, and 3.5 minutes for thin film modules using a fast cure EVA. The idea here is to increase the temperature to accelerate the reaction and reduce the process time. However, such a short time with no defects and full curing of the encapsulant is quite challenging to achieve. In enquiring about this aspect of its new machine, pv magazine received no comment from the company.
However, Tekni Solar later reached us and mentioned that its Robostak Gen V laminator boasts 0mm edge pinch on GG modules, and thickness deviation (edge flare) of up to 70µm. It further added that with trials on field and further optimization, it has able to reduce the cycle time for GG module lamination to 200 seconds, which is less than 3.5 minutes. If holds true, this is the fastest lamination process in the market, achieving production of 72 GG and 80 GB modules per hour.
Giving more information about the process benefit, Tekni Solar official said, “All of this, with no edge distortion or skewing/sliding of layers in the module, no edge pinch, no encapsulant outflow, no significant downtime, no silicone membrane or other materials subject to wear and frequent breakage – meaning no scrapped panels due to defects or membrane breakage during the cycle, less downtime, possibility of eliminating the need for edge trimming, and longer life span of modules. All of these points can add up to big savings for solar panel manufacturers.”
Therefore, there are several factors to consider with the lamination process. Key among them are ensuring adequate time for evacuation, the proper melting of encapsulants up to a certain level (typically 120°C) before transferring to the curing stage, ensuring enough curing time to achieve more than 90% curing (recommended by EVA suppliers for better module reliability nowadays), and effective cooling without creating stress or bowing of the module. Every step is critical.
Moreover, the market is ushering in new materials like PO, which has limitations regarding temperature: A higher temperature usually degrades these materials. Additionally, the thickness of the glass used in GG modules is not standardized, varying between 2 mm and 3.2 mm, and for thin film between 1 mm and 2 mm.
Thick glass can reduce heat transfer rate, resulting in a longer process time. So with the news that Meyer Burger has shuttered its lamination line, and with the growing emergence of Chinese suppliers, it will be interesting to see what the future holds for Europe’s firms operating in this increasingly competitive space.
This article was amended on April 26 at 15.30 to include comment from Teknisolar.
This content is protected by copyright and may not be reused. If you want to cooperate with us and would like to reuse some of our content, please contact: editors@pv-magazine.com.
We intrestead to puerchesh solar energy farm. We having 1800 vigha land in near Vadodara.