Crystalline silicon (cSi) cell manufacturers saw a lot more stability in 2017 than in the previous year, with only marginal price declines registered, and stronger-than-expected demand, particularly in the third quarter when prices actually increased, particularly for mono-cSi products, which have continued their march to higher market share. “The two main reasons for this stable cell price were the higher cost of raw materials and wafer, and strong demand paired with limited availability of monocrystalline wafer,” explains Karl Melkonyan, Senior Analyst, Solar Demand at IHS Markit.
“Component prices in 2016 were driven by oversupply. In contrast, the supply-demand market in 2017 was relatively healthier and experienced moments of supply tightness, adds Jade Jones, Senior Analyst, Solar Markets at GTM Research. “Prices were able to exhibit healthier trends in 2017 because downstream demand in China was a lot more stable quarter-over-quarter. As the largest PV market in the world, accounting for over 50% of installations in 2017, China’s seasonal demand trends have a huge effect on supply-demand trends.
No surprises
China, of course, remained both the biggest producer and customer for silicon cells, with its June 30th Feed in Tariff deadline and the Top Runner Program the key drivers for demand throughout the year. With its stringent efficiency requirements, China’s Top Runner Program has also been the main factor in the growth of mono-cSi technology. “Around 4.5 GW was installed as part of the Top Runner Program in 2017, and mono-cSi, mostly mono-PERC, accounted for more than 70% of the total,” says Independent Solar Analyst Corrine Lin. “So the Top Runner Program really pushed China to become the biggest mono-cSi cell demand country in the world.”
Analyst expectations for the coming year are broadly in line with what happened in 2017. “Similar to previous years, the FiT cut will result in cell demand peaks a few months ahead of the June and December deadline, says Melkonyan. “Demand for monocrystalline products will peak in the second half, when most Top Runner program projects will be installed.”
One of the biggest announcements to come out of China in 2017 came in November, when Tongwei Co Ltd said it would invest $1.8 billion in two new cell facilities located in China, a move that will make it the world’s largest cell producer by some margin. IHS Markit, however, is muted about the effects of this announcement, at least for the coming year. “the short-term impact has been small since the new capacities will be added step by step, based on real situation and demand on the market,” says Melkonyan. “The first phase will not be on board until the second half, which means its impact will not be so strong this year but it should have a greater impact from 2019.
For the remaining cell manufacturers outside of mainland China, however, Tongwei’s announcement could spell bad news. “Tongwei’s huge expansion plan shows a seriously aggressive manufacturing cost reduction,” says Lin. “Since they are the biggest & lowest cost cell supplier, Taiwanese producers could end up losing their market share faster than they imagined.”
Taiwan turmoil
Formerly the undisputed leader in high-efficiency concepts such as PERC, Taiwanese cell producers struggled to keep up with cost reductions and economies of scale over in mainland China. “Taiwanese cells are known for good quality, so could demand a slightly higher price before 2017,” explains Corrine Lin. “But Taiwanese producers were conservative in investing in production line expansions or upgrades from 2015-2017. So, in 2017, Taiwanese cell did not have the best cost/performance ratio anymore, and module companies did not want to pay a premium price for Taiwanese cells. As of 2017, there is no efficiency or price gap between Taiwanese and Chinese produced cells.”
IHS Markit also notes that the Taiwanese cell makers have begun to pursue alternative strategies to competing on international cell markets: “Margins for cells were low last year, especially for Taiwanese cell producers,” says Melkonyan. “Taiwanese producers have, for the most part, increasingly focused on their domestic market and attempted to expand into module manufacturing rather than focusing exclusively on the merchant cell market.”
This change in strategy is evidenced in the October announcement that three of Taiwan’s largest cell makers – Neo Solar Power, Gintech, and Solartech – would merge to form one company under the name United Renewable Energy Co. Ltd. This move will combine the expertise of all three, and to move further downstream into module assembly and project management, whilst maintaining significant wafer and cell capacities. “The establishment of UREC will allow Taiwan’s solar cell industry to get rid of its role as foundries and further urge the green energy industry to root and grow strongly in Taiwan,” reads an October press release announcing the planned merger.
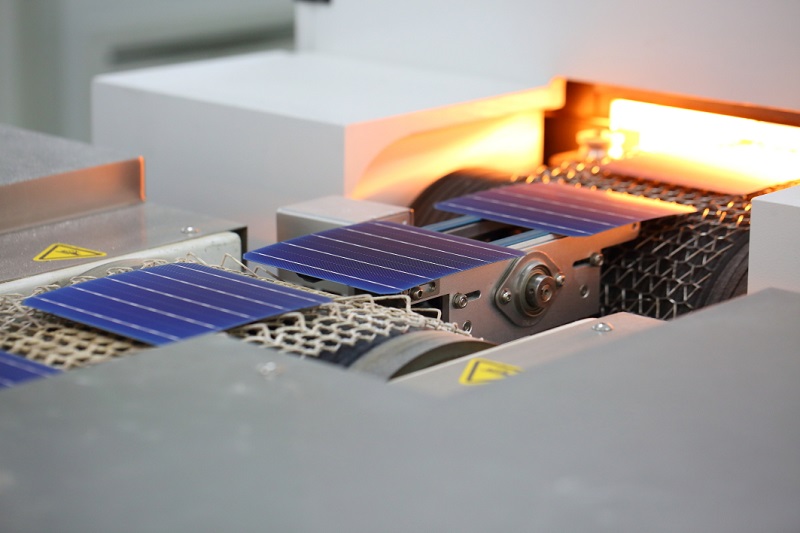
Farther afield
With the top 10 spots (ranked on 2016 production) taken up entirely by companies based in East Asia, predominantly China, it remains to be seen whether any other region could achieve significant levels of cell production. Cell production is one of the most technologically difficult stages of PV manufacturing, with very high capex requirements, so it is difficult for new players to become competitive, and existing manufacturers are conservative when it comes to risks such as those presented by moving into a new region.
Much has been said about India’s efforts to build its own solar manufacturing industry, and how this could benefit the country’s enormous renewable energy ambitions. For now, though, the country remains well behind the East Asian region. “There was some capacity growth in India, from small additions (e.g. BHEL’s 200 MW cell and module ramp) to larger GW expansions like that of Adani,” says GTM Research’s Jade Jones. “While many major Chinese suppliers have previously expressed interest in expanding manufacturing in the region, most held off in 2017.”
“Since cell efficiency and cost is hard to control to the same levels achieved by Chinese or Taiwanese suppliers, adds Corrine Lin, “India still imported huge volumes of both modules and cells in 2017.” Further into the future, however, analysts are more upbeat about India’s prospects as a manufacturing center. “I believe that yes, with time we will see some major developments in India – also on the cell side,” says Melkonyan.
In 2016, capacity expansions in South East Asia – primarily Malaysia and Vietnam – emerged as a major theme among cell producers, as they sought to avoid trade tariffs raised on goods exported from China to the EU and U.S. This trend continued in 2017, albeit at a lower rate, and looks to have run its course in 2018, as the U.S. has now broadened its trade tariffs to include countries beyond China and Taiwan, and the existing capacities in SE Asia are sufficient to meet the rest of the demand. “Some acquisition and expansion happened in South East Asia in 2017,” says Melkonyan. “However, we do not forecast any big expansions or new capacities in 2018.”
According to figures from GTM Research, total cell capacity in Southeast Asia increased by around 28% YoY in 2017, reaching more than 30 GW. “Southeast Asia remained an important region for suppliers shipping to the EU and to the U.S.,” says Jones. “Expansion continued in regions where major Chinese suppliers had already started building their tariff-free fabs.”
Technology trends
Mono-cSi products continued to gain market share in 2017, and analysts expect that as much as 40% of the cell market in 2018 could be mono products, predominantly mono-PERC. “We expect mono will keep increasing further in 2018, at a rate similar to 2017 or stronger,” says Karl Melkonyan. “The clear trend is toward mono PERC, followed by increasing number of n-type, with expansions of the existing players, as well as newcomers.”
The rise of PERC as a mainstream technology, first observed in 2016, continued into last year, and is the main reason for the increased market share of mono cells. Corrine Lin estimates that in 2017 around 18 GW of new PERC capacity was added – bringing the global total to 33 GW, from just 15 GW at the end of 2016.
Analysts expect PERC, both in mono and multi-cSi cells, to continue its growth in 2018, particularly thanks to the newly extended Top Runner Program in China, and broader demand for high-efficiency cells and modules. Though n-type technology has also begun to rear its head, it is still not regarded as a mature technology, and is expected to stay waiting in the wings once again this year.
“Looking into 2018, producers are going to focus on increasing capacity of the high-efficiency products that they started scaling last year, such as multi and mono PERC. With a strong focus on increasing product power, some producer will turn to ramping up internal bifacial capacity to GW levels,” says Jade Jones. “Beyond cost competitive high-efficiency cell technology, we expect the vast majority of suppliers to continue working on N-type R&D efforts rather than scaling commercial capacity.”
This content is protected by copyright and may not be reused. If you want to cooperate with us and would like to reuse some of our content, please contact: editors@pv-magazine.com.
Hello Mark
My name is Meir Bittan. I am working at Lumos-Global from Israel.
I am interested by cell size analysis, mainly the 156×156 vs 125×125.
Questions:
– What is the market share?
– What are the production/installation trends?
Do you have such analysis?
Thanks
Who number 3