From pv magazine 04/2020
Part of your work in the UNSW PV team is to continue some of the research of PV pioneer Stuart Wenham. On a personal or even institutional level, how is his loss continuing to be felt?
Personally, I knew Stuart since I was an undergraduate and he was a big personality – he was the lecturer you would remember. He was passionate, he knew his stuff and always had time for his students. I went on to do my PhD on buried-contact solar cellgroups, which was the technology he had done his PhD on, so again I got to work with him and learn from him.
He was passionate about what he did – particularly where that would be helping the industry, and he really bridged the gap between the industry commercial and the academic side of research. It enabled the sharing of information both ways, which is beneficial to all involved. He had set up a whole network of contacts across the globe and worked relentlessly at maintaining that.
When he passed away [in December 2017] it was very sudden and any plans he had to fully pass on that know-how and knowledge could not happen in the way he would’ve liked. So it has been difficult, everyone does their best, but it is a big loss.
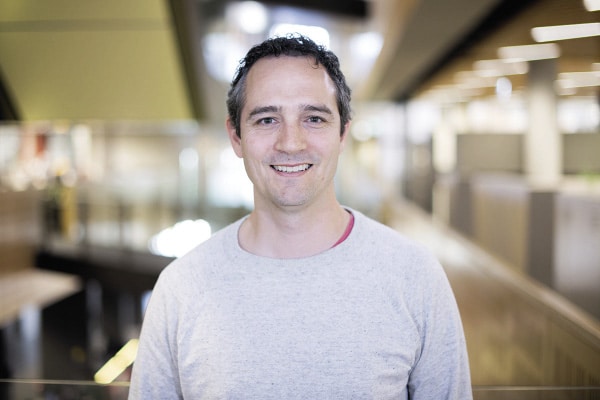
Professor Wenham’s pioneering research into LeTID was one of his last academic areas of inquiry. How is the work progressing?
What Stuart did leave us with is a lot of momentum, funding, and a great team of people who were working on a lot of his ideas. His work has continued in many ways, particularly on the fundamentals of LeTID, ways to mitigate it, and following up on the big unanswered question of exactly what defect could be causing LeTID. He encouraged individuals to have their own ideas, and that culture has been maintained. And so, over time, his legacy is branching out in many different directions.
Of course, Stuart had so many ideas that there are still many we have not had a chance to investigate, things that he would have been pitching to the team three or four or five years ago. He was prolific, he would always put his thoughts and ideas out there and we are only now getting around to investigating some of them.
How would you describe our understanding today of how LeTID manifests itself?
It has changed a lot over the years. From an industry perspective, when we were first observing LeTID, we would characterize it as being 10% degradation over a long timeframe, representing a massive hit on the energy yield. As we’ve studied it, that has been reduced a lot.
Studying LeTID now on current industrial solar cells, we would say that it represents a 1-2% degradation on a cell or even less, and sometimes industry partners prepare study samples that are completely stable – which actually makes it hard for academic research.
From an academic point of view, there is consensus that it is related to hydrogen, or more specifically an excess of hydrogen. Hydrogen is interesting in all the different ways it can behave; it can bond with things, change its charge and its position in the cell. It can also change in response to things like temperature and light. This leads to a wide range of behaviours. Ultimately, it appears that what the impact of hydrogen does in the cell comes down to how producers process the sample. And there is still a lot of work in trying to nail down the details of that and ultimately removing LeTID completely. I wouldn’t say there is 100% consensus on what the exact defect is that causes the degradation, but there is agreement that hydrogen has a significant role to play.
How universal would you say the methods to avoid LeTID are in the industry today?
It comes down to processing and it is almost analogous to making a good solar cell; if your processes are good and you do it well, then you can produce a high efficiency cell, which is also true of stability. Understanding how to test is important as it allows top quality manufacturers to process things repeatedly in a way that the cells are stable. There is an underlying factor in the nature and quality of the wafer bulk material, but the biggest factor is the processing.
So then, what is the LeTID fix that you see most commonly in use? I remember UNSW was promoting a method in partnership with a number of equipment suppliers some years ago.
High intensity light and elevated temperature can start to drive the hydrogen away from the bulk. Current injection after the cell has been produced has also been popular in that manufacturers can stack the cells and run the process on a lot of them at once.
But avoiding LeTID hasn’t just been about applying a post-process mitigation strategy. As I’ve mentioned, it is also done by optimizing the manufacturing process – the details of how companies have done this is not something that gets published. We know that if you change the amount of hydrogen in the nitrides then that changes it [LeTID] and the firing to form metal contacts that also have a big effect. There really are a lot of handles that the industry can pull with LeTID.
What is interesting is that hydrogen was always our friend, it healed the defects, the cracks, it was there to help. And because of this it was thought that the more hydrogen the better. Then when LeTID was discovered, it became understood that what you need is the right amount of hydrogen; too much and it becomes a cause of [charge electron carrier]recombination.
And at the end of the day, it’s understood that modules suffering from LeTID will actually regenerate after something like five years, under relatively hot conditions. Is that right?
That is correct, LeTID is a cycle of degradation followed by recovery although the full cycle is expected to take many years in the field. Interestingly, over the years there have also been reports of surface degradation and this is something that can occur after the LeTID cycle. You can get a degradation and recovery of the bulk lifetime, which is then followed by degradation of the surfaces.
The amount of surface degradation that can occur can be much worse than LeTID, even particularly in cell architectures with higher efficiencies. What we need to understand are the fundamentals of what is causing that.
So far most of the reports [of surface degradation] are on test structures rather than cells and although we can make it happen in our labs, with some industry samples we typically can’t get this sort of degradation to happen. So, I would be surprised if this problem existed in current commercial solar cells. However, it does seem to make sense, if there is lots of hydrogen, the wafer surfaces are lightly doped, and particularly when there is a thermal oxide with thin silicon[passivation] layers, surface degradation can occur as the hydrogen moves from the bulk to the surface where it accumulates and causes a problem. That is something we need to be watching for as device designs evolve and it is worth pointing out that this needs long timescale testing to be detected.
At UNSW we try to dig into the fundamentals of why these types of problems are happening at a deep level. It’s the kind of thing the industry doesn’t have time to explore. What the industry does is optimize the cell architecture and try to control the problem. At the university, we can develop a deeper understanding [of degradation mechanisms] so as to be able to develop better longer-term solutions.
This content is protected by copyright and may not be reused. If you want to cooperate with us and would like to reuse some of our content, please contact: editors@pv-magazine.com.
It is clear, if not clearly evident, that the most distributed and quantity of Energy, by far, is Solar Energy…
If it is distributed and so are the consumers…. and ALL require an Electric Grid…. why does one need Hydrogen… except in niche Industrial Complexes providing and serving adjacent Industries….
The Electric Grid is the only “obvious” solution for distributing energy… Directly, Safely and Economically… and Hydrogen fails in ALL THREE PARAMETERS as compared to an Electric Grid that delivers Clean Energy to Users Site for Direct Use… or convert to Hydrogen near point-of-use…. to ensure Public Safety too…
Proponents of “InterContinental and other Pipelines remain… mum… silent… about Safety of Handling and Transportation of Hydrogen… it was just a small spark…. that “killed” the Hindenburg about 90 years back… when will we ever learn….!!!
Now with respect to use of Ammonia in Coal Fired Plants… does combustion of Ammonia or even other fuels not prodice NOx… a “Polluting Gas”…. if we ready have Abundant, Sustaibable, Clean and Green Solar Energy producing
Electricity directly…. why does mankind need ANY POLLUTING FUELS… to produce Electricity…. whether Fossil, Nuclear, Hydroh
gen, Ammonia or other “exotic fuels”…. These are ALL diverting attention from eliminating Pollytion… asap…