pv magazine: Please tell us about your scope of work in India.
Justin Lemmon: We have three primary business lines. One is first-life battery packs, where we make batteries with new cells. Two, second-life battery packs, where we take used cells and then refurbish them into new batteries. Then our third line is for the batteries that have no useful life left in them. There we recycle the batteries so that all those battery materials and chemicals can then be reused into new cells going forward.
We are essentially trying to create a circular loop for the battery supply chain wherein we do everything except for the cells.
Currently, we operate two co-located factories of 200 MWh for manufacturing Lithium-ion batteries, and 300 MWh for recycling the batteries. We plan a 3 GWh integrated lithium-ion factory for the next phase of our expansion as we see tremendous growth on all our business lines, not only in India but from our customers abroad as well. Out of this 3 GWh, 1 GWh will be allocated to manufacturing of first-life and second-life batteries, and 2 GWh to recycling. With several locations being considered, it will be India’s single largest, single-location Li-ion battery manufacturing and recycling factory. In addition, we will use our facilities in India as the blueprint for our US facility in 2022.
What’s the business and consumer case for second-life batteries?
One obstacle to electrification, particularly in developing economies, is cost. The second thing is very complex supply chains as far as battery materials are concerned. The supply chain adds economic and strategic cost due to the importance of the raw materials that are only available and refined in a few places globally. So, if you look at our technology, we’re trying to solve both of those challenges.
Essentially, we are lowering the cost of the battery. Most of the batteries can last much, much longer than their anticipated life. Let’s say the battery in a four-wheeler EV, or even a stationary application, lasts for 8 to 10 years in its first life. At that point, the battery can either be re-used or recycled. We can take that battery [at the end of life] after its first application, test the battery to meet our safety, performance, and warranty requirements, and move it to a new [low-power] application wherein it could last for at least another three years. That obviously provides a power solution but at a much lower cost.
Whatever is coming in, whether from a vehicle or a stationary application, we’re able to test it and determine its best application. One fortunate thing going for India is that it has essentially the largest low-power mobility market in the world, from a two-wheeler and three-wheeler combination standpoint. And it will grow significantly over the coming years. That is unlike any other market in the world outside of maybe China. So, if you compare that to the US, it has lots of [electric] cars [on the road], but not much of a low-power [mobility] market.
It’s not only the low-power mobility applications that present huge gigawatt-hour markets in India. Most of the stationary side applications, whether the residential storage, mini-grid, or other power backup solutions, are also low-power applications.
From the performance standpoint [of second-life batteries], we have been doing second-life batteries for almost three years. At this point, on the mobility side, we have collected almost 2,000,000 miles of operational performance data from these batteries and that’s so that we can continue to test the performance of a particular cell and module in that application and refine [our process] to find the best solution.
We are seeing that at least 50% – 60% of the batteries coming out of EVs or stationary applications like mobile towers are still usable for different applications—say, in a low-power application for at least another three years. And that creates a market dynamic that doesn’t exist in other geographies.
The idea is to create a battery that meets all the performance requirements for a particular application, lasts at least three years, but costs 30% less than a new battery. And that’s a real game-changer. If we can solve for cost, developing countries stand to gain significantly more from battery power than developed countries.
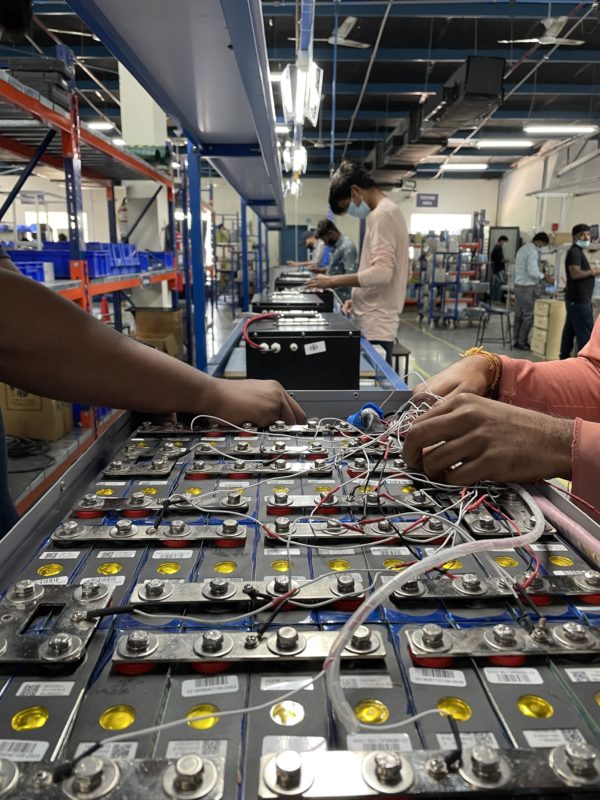
Image: Lohum
What all battery chemistries will your facility be equipped to recycle? What recycling method will it use?
On the material side, we’re solving the supply challenge through recycling. As I mentioned before, our recycling technology can recover all of the materials in a battery, both on the cathode and the anode side. From a design standpoint, we recycle every chemistry, every form factor. If you have good enough recycling technology you can recycle the materials in both the cathode and the anode. This capability enables you to produce all the materials and the chemicals in a battery composition that can be then sold back into the battery cell supply chain.
Talking about the recycling process, think about it in two building blocks. One is mechanical separation. Here, essentially the used battery gets shredded. And then the electrode material is separated from the rest of the materials such as steel and plastics. The electrode material is considered black mass, and that’s where all the cobalt, lithium, manganese, graphite, and other valuable battery chemicals reside.
The next phase of our recycling process is hydrometallurgy. It involves a series of steps, where we use a low-power chemical process at almost room temperature.
The process is capable of 95% yield. And then on the output side, the composition is individually separated chemicals like cobalt, lithium, nickel, manganese, and graphite, which are all battery grade.
In India, lithium ferro phosphate (LFP) batteries are predominantly used. What will be your preferences in recycling?
There’s going to be a lot of LFP batteries coming through the pipeline, but I think the issue is just that it’s not super valuable at this stage—and so, people haven’t focused on it too much at all. At this point, there’s tons of additional volume where you have nickel chemistries and that will be the high focus area for the foreseeable future. We do recycle LFP batteries and conduct continuous R&D to continually improve the recovery process since they will be an increasing source of feedstock.
Do you intend to supply the recovered chemicals/materials to other battery manufacturers too?
We already sell material to battery manufacturers and the volumes will only increase over time. Our goal is to become the largest producer of battery materials in India and other major global geographies drawing on our capability and capacity to recycle. India lacks many of the key materials required for battery manufacturing. So, the best way in the near term for India is to generate raw materials through recycling.
The battery chemistries are still evolving. Does that mean uncertainty in terms of securing the entire supply chain for raw materials?
Until there’s a major leap in battery chemistry, which is probably five to seven years away, you’re going to need lithium, nickel, cobalt, and also graphite for sure. India only has graphite. All the mobility applications are at this point mostly high nickel content.
While the manufacturers are continuing to lower the percentage of cobalt in the cells, it’s going to be hard to get away from it altogether as you have to have cobalt from a safety standpoint for high-energy-dense applications. LFP is, however, showing a lot of promise for certain ranges/energy density due to innovation and will be introduced in more applications. Lastly, as for graphite, India does have graphite but the challenge is it doesn’t have a refining capability for graphite. For graphite to be used in a battery, it has to be super high purity (99.9% and above). And the most important, and also the most difficult part is it has to be shaped, spheronized, and coated to make it suitable for battery manufacturing. That refining process right now exists pretty much only in China. So, in addition to producing battery raw materials through recycling, there is an opportunity for India in terms of adding that refining capacity.
This content is protected by copyright and may not be reused. If you want to cooperate with us and would like to reuse some of our content, please contact: editors@pv-magazine.com.
Very interesting, we need article like this, very useful, thank you