From pv magazine 04/2022
Moving into its second phase, our project is focused on the analysis of additional rooftop PV array sites in India. We are also diving into the detailed causes of cell cracking by scrutinizing the logistics and mounting structures of PV plants. Preliminary results from 15 on-site inspections performed in the Indian cities of Jammu, Ahmedabad and Nagpur at the end of 2021 show that the low performance of the inspected PV plants was caused by a combination of module cracks, near shading, soiling and module product defects.
As in the first phase, the main objective of the study was to quantify the causes of underperformance, defining them in terms of contribution to loss in generation, and to propose cost-optimal solutions to address the quality issues. The results of the study are being obtained thanks to the joint work carried out by a consortium formed by the following companies: (i) PI Berlin as lead consultant; (ii) Mitsui Chemicals India Pvt. Ltd overseeing the evaluation of PV modules in the field and in its laboratory in Ahmedabad; (iii) Aerocompact Pvt. Ltd in the role of visual inspector of system components other than the PV modules; (iv) Expectus GmbH as adviser for the logistical aspects of the plants under construction; and (v) Above providing digitization tools to centralize information obtained in a single platform that includes the digital twins of each of the plants.
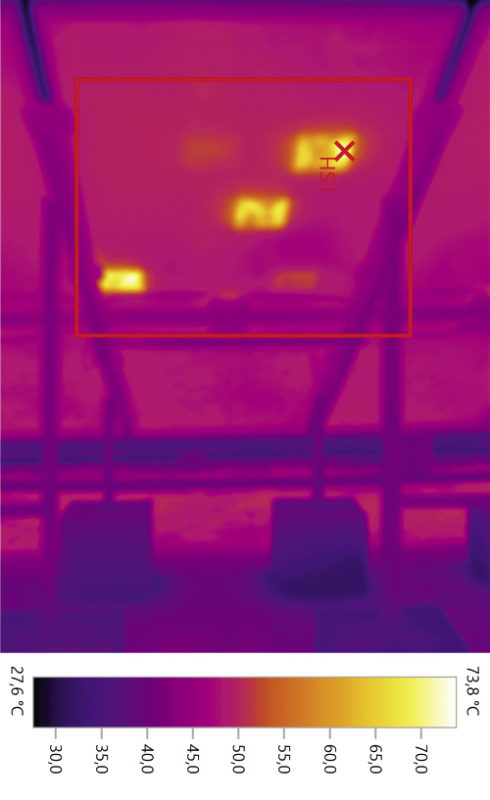
Ahead of each visit, the available documentation was reviewed in order to maximize the efficiency during the site inspection. Using these documents, a digital app-based checklist was prepared through Above’s EyeSite mobile application to optimize time spent on-site and maximize accuracy during the on-site inspection. The site inspections focused primarily on direct impacts on the performance, such as cleaning, module degradation, shading, inverter unavailability, logistics aspects, and O&M considerations. Safety issues, without a direct impact on the performance, were also documented.
The assessment of the logistics was primarily focused on the evaluation of the module handling at key stages such as truck loading in the factory, transport and unloading on site. The objective of this methodology is to identify at which point in the transport phase the damage occurs and to demonstrate that in many cases this leads to power losses in the modules. It can be observed how PV plants with difficult access to the roof imply a higher incidence of damage at the module level.
Quality control
One of the innovations introduced in this second phase is the incorporation of a digitization tool that allows the creation of a digital twin of each plant. This twin represents each of the plant components and through a purpose-built smart app (EyeSite) the inspection teams are empowered to conduct site inspections using a mobile or tablet. In this way the ground-based data collection and processing times were accelerated by systematically capturing, collating and storing inspection data within Above’s “SolarGain” data and analytics platform. Part of the data uploaded on the platform are photographs of the PV modules, pictures taken with infrared cameras and images obtained by means of the electroluminescense technique.
Underperforming modules (due to higher degradation rates and possibly early stages of potential induced degradation) could lead to a yield loss of 15% at the system level. This rapid degradation could be explained by a PID sensitivity of the PV cells in the installed modules, in combination with the typical hot and humid conditions. The presence of bird droppings, debris, or pollution, result in soiling losses as high as 22% for some of the systems. According to PI Berlin’s estimations, in some of the inspected PV plants, the losses caused by near shading exceed 7%, while self-shading exceeds 8.5%. In PV plants with severe mechanical damage at the module level, the nominal power of the PV plant can be reduced by up to 8%.
To avoid these types of defects in the next generation projects, PI Berlin recommends a number of commissioning tests, training of operators, proper assessment of the module cleaning frequency or proper definition of the EPC responsibilities.
In addition to these preventive measures, PI Berlin proposes four affordable revamping and repowering measures to partially mitigate the negative consequences of the findings described in the previous section by boosting energy production. These are the (i) improvement of module cleaning frequency, (ii) resorting of modules and strings, (iii) module replacement, and (iv) a higher albedo factor. Depending on the status of each PV plant these actions may lead to a performance boost between 5% and 35%. Furthermore, these actions do not require large investments in the opex.
Asier Ukar is a senior consultant at PI Berlin and managing director of its Spanish unit, PI Berlin S.L. He has 14 years of experience in the deployment of rooftop and multi-megawatt, grid-connected PV systems, with a physical presence in Europe, Asia, Latin America, Africa. He has been active in the Indian market since 2010 and has been involved in the design, supervision and refinancing of approximately 5 GWp of installed capacity throughout the world since 2007. Since 2008, Ukar has worked as a consultant for banks, lenders, asset owners, state authorities and developers. He holds a diploma in mechanical engineering and speaks five languages.
This content is protected by copyright and may not be reused. If you want to cooperate with us and would like to reuse some of our content, please contact: editors@pv-magazine.com.
By submitting this form you agree to pv magazine using your data for the purposes of publishing your comment.
Your personal data will only be disclosed or otherwise transmitted to third parties for the purposes of spam filtering or if this is necessary for technical maintenance of the website. Any other transfer to third parties will not take place unless this is justified on the basis of applicable data protection regulations or if pv magazine is legally obliged to do so.
You may revoke this consent at any time with effect for the future, in which case your personal data will be deleted immediately. Otherwise, your data will be deleted if pv magazine has processed your request or the purpose of data storage is fulfilled.
Further information on data privacy can be found in our Data Protection Policy.