From pv magazine Global
pv magazine: REC just introduced your newest module, the REC Alpha Pure-R. Its predecessor, the Alpha Pure, picked up the Intersolar Award this year in Munich. I understand that the fact that you were able to eliminate lead was a major reason the jury selected the module as a winner. How would you describe the module’s features?
Cemil Seber: The REC Alpha Pure-R integrates G12 wafers, with heterojunction (HJT) technology, half-cut cells, and we’ve maximized power in compact a format as possible with gapless interconnection. And as with every Alpha product it comes with the advantages of HJT technology, like high efficiency and a low temperature coefficient. With the compact size and two support bars, it means that customers can have a good feeling about the warranty – including with heavy snow or wind loads. We really feel we’ve hit the sweet spot in terms of aligning what is best with efficiency, size, sustainability, and on the usual product specs that everybody uses to benchmark PV panels.
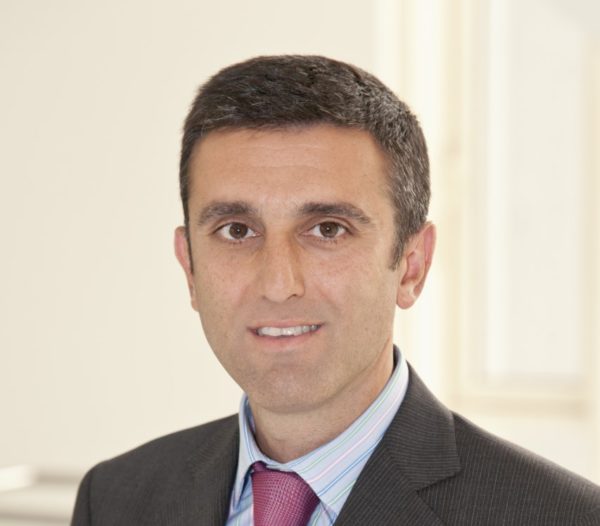
Image: REC Solar
I mentioned lead-free, how was it that you were able to do away with all lead entirely?
Some lead can be in the silver paste, but we use lead-free paste. Additionally, we are now using innovative solder-free foil and wire combination, eliminating again the lead-content here. The other place where lead is being used is on the cross connectors, where the lead is used for the soldering. Also, in the JB [junction box] lead is used for the solder. In the Alpha Pure-R, the cross connectors aren’t soldered with lead and there’s no soldering in the JB with lead. These things are easier said than done. But we reduced the lead in the Alpha and now we’ve eliminated it with the Alpha Pure Series.
The foil interconnection was called “busbarless” some years ago. Of course, initially, REC worked with Meyer Burger with the Smartwire technology. How have you moved forward without Meyer Burger on the cell interconnection?
We’re expanding our initial HJT production from 600 MW to 1.2 GW, and for the expansion we’re doing that with equipment that is not from Meyer Burger. REC has worked intensively for many years with its key suppliers to develop other methods that will still be foil and wire based, proprietary to REC.
Looking more closely at the expansion, Meyer Burger also provided the deposition tooling for the HJT cell production. How will you move forward without Meyer Burger providing support and the production equipment?
We have run more HJT cell production than anyone in the world successfully; we have produced close to 1.5 of HJT and have successfully put that on the market. You also have to remember that REC has been in the PV industry for 25 years. We had skeptics with the first Alpha [HJT] modules, but we’ve proven them wrong. HJT also has less processes than other cell technologies and when you have good process control you can have very stable production. The part where REC really excels is in the industrialization of these new technologies and we have a head start. We launched Alpha with HJT in 2019, so we did it 2.5 years before anyone else.
And where will the expansions beyond the 1.2 GW in Singapore take place? We have heard of a facility in France for some time now. And, of course, since REC’s acquisition by Reliance Industries, Indian manufacturing is also an option.
We were acquired by Reliance on December 1, 2021. And with regards to PV, we are the cornerstone of what they want to do. Singapore has been the center of excellence for REC and it will continue to be that way. We had 600 MW of Alpha Pure HJT production capacity and we are adding another 600 MW of Alpha Pure-R. We are currently working on that expansion plan for Singapore – and in August that production capacity will be operating.
In India, we are building cell and module capacities at gigawatt scale. Reliance is looking both upstream and downstream and wants to deploy in the hundreds-of-gigawatts of PV. Of course, REC will be supporting the expansion in India. Outside of that, we have our two main markets: the U.S. and Europe. And right now we are in the planning stages and considering our options in both of these regions.
Can you give me a bit more detail on the French factory?
What we can say is that we are in the planning stage and there are multiple scenarios for what we can do. There are geopolitical dynamics which are favoring manufacturing in both Europe and the U.S.
What about further upstream to wafers or even polysilicon – because this is where REC in Norway has its heritage?
We have a strong expertise across the whole value chain, from silicon in Norway up to modules in Singapore. This expertise is critical in order to control all processes and ensure high quality of the final product and it’s a strong value in our expansion plans.
Turning back to Europe, there seems to be a lot of energy in the market at the moment – for installations and manufacturing. What’s your message for the market?
I think a key message is: “We’re growing and we are hiring!” We need to enjoy the moment also. REC has launched a new product and we have bigger plans and some of those plans are very concrete and we are talking about them openly. Others are in the scenario planning phase. Our focus is HJT, and our future is in HJT.
This content is protected by copyright and may not be reused. If you want to cooperate with us and would like to reuse some of our content, please contact: editors@pv-magazine.com.
Nice and informative article