From pv magazine Global
Italian startup Tialpi Srl has developed a new concept for photovoltaic panel recycling plants that may reportedly help recycle at least 85% of a photovoltaic panel’s weight.
“We have developed a new technology to recover the most significant components of photovoltaic panels such as aluminium profiles, copper cables, and glass,” Vera Ramon, who is responsible for energy at Tialpi Srl, told pv magazine. “Our next step, which is the second phase of our project, will be completing the development of the processes for dividing the backsheets from the wafer of silicon, which will make it possible to recover 100% of a module’s weight. For the first phase, the company has already secured a patent while for the second the patent is still pending.”
The second phase of the project is currently under development at the company’s facility in Mottalciata, in the Italian northern province of Biella. The industrial plant will recycle solar panels across several steps.
The process initially moves the panels into the line from two vertical stock containing about 25 panels each via a gripping system with pneumatic pistons that presses on the four aluminum perimeter profiles, which are then transferred through wheeled containers to the stock with a forklift. “The connector cables are cut manually with a simple scissor and the cables will be bagged manually directly into big bags on a pallet to be then transferred to the stock with forklift,” said Ramon. “Then the edges of the aluminum frame are cut by means of four miter saws operated automatically and the dust generated will be sucked up with a vacuum cleaner and bagged directly into 25 kg bags.”
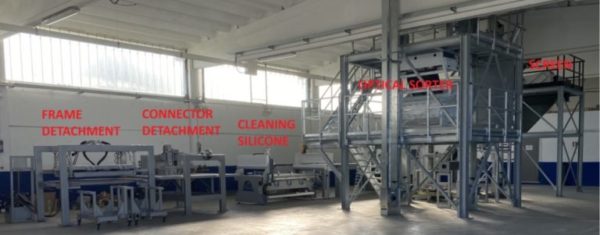
Image: Tialpi
In subsequent steps, the process detaches the aluminum frame by means of four pistons, then removing the electrical connectors fixed to the backsheets by cutting the silicone or other sealants using a thin semi-hardened steel blade. Machinery moves the treated panel to one of two glass detachment lines, where the glass is heated by infrared lamps and then detached via a vibrating steel blade. “The action of the vibrating knife and the detachment from the sandwich crush the glass that falls on a lifter and moves on to the next section,” explained Tialpi’s Ramon. “The sandwich is conveyed to a pallet, with gradual lifting, which contains up to 500 sandwiches, for a height of about one meter and a weight of about 1,500 kg.”
After this process is completed, a rubberized cup belt transports the glass to the screening department. The purpose of the screening is to eliminate fine (<2 mm) and coarse (> 10 mm) glass elements and any sandwich residues to obtain glass sized between 2 mm and 10 mm. These two products are then bagged directly into big bags on a pallet to be then transferred to the stock with a forklift.
In order to obtain a high-quality glass, the two products must then be properly stored and optically sorted to identify and reject non-transparent particles. “After the optical sorting, the final high-quality glass with a 2-10 mm size is directly stored in a 50-ton capacity silo. From here, it is possible to load directly the trucks for final delivery to the customers,” said Ramon.
The final step consists of an offline machine that is manually fed cabling at up to 150kg/hour to treat and extract copper with 99% purity, and plastics that can be used for extrusion. The whole process, according to the company, is environmentally compatible, as it is carried out without emissions into the atmosphere and without the use of water. The recovered aluminum can be used in remelting processes for various industries such as automotive and construction, while the high-quality extra-clear glass can be utilized in the container glass and flat extra-clear glass industry.
According to its developers, the entire process has a low energy consumption of about 1kW per panel. “It is carried out with only two workers and the payback time is about two years,” the spokesperson explained.
The company developed the special design in the frame of the “Frelp By Sun” project, which was initially funded by the European Union. The project began in 2012 with the aim of testing and developing innovative technologies for 100% recycling of end-of-life photovoltaic panels in an economically and environmentally sustainable way. The project leader was Tialpi’s parent company, Sasil, a unit of Italian mining company Minerali Industriali, in partnership with glass maker Stazione Sperimentale del Vetro di Murano (SSV) and the consortium PV Cycle.
This content is protected by copyright and may not be reused. If you want to cooperate with us and would like to reuse some of our content, please contact: editors@pv-magazine.com.
Would like to association with R&D team for PV module recycling technology