At the Intersolar India 2024 in Gujarat, several solar manufacturers in India spoke with pv magazine. Most have started TOPCon module production and are getting a good response from the market. TOPCon is expected to command almost 50% market by the end of this year.
While TOPCon cell capacities are underway by some manufacturers, these will be insufficient to cater to the current requirements of domestic module manufacturers.
The lack of domestically produced cells is a challenge even for mono PERC module manufacturers. This limits the market for domestic panel manufacturers as government projects under the Ministry of New and Renewable Energy’s schemes and programmes mandate cells to be made in India under the domestic content requirement.
The cell manufacturers in India have been prioritizing domestic cell production for in-house module manufacturing or exports, particularly to the US market, exacerbating the scarcity of cells for domestic projects.
“While the demand for domestic mono PERC solar cells has surged due to government utility-based tenders and subsidy schemes, the domestic manufacturing capacity has not kept pace, leading to a significant demand-supply gap. This has resulted in the cost of domestic solar cells being more than two to almost three times that of imported A-grade cells, despite the wafers for cell manufacturing being sourced internationally. Adding to the complexity, India cells are about 20-35% costlier than imported cells having the same wafers. This discrepancy has put module manufacturers, especially those without their own cell production lines, in a difficult position, making it challenging to meet the demand for DCR modules effectively,” Anurag Garg, CEO, Jakson Solar Modules & Product Business, told pv magazine.
“With p-type mono PERC cell (M10 size) as the current dominant technology in India and n-type cells gaining traction, there is an evident need to expand production capacities. The industry is gradually moving towards technologies like TOPCon, which is upgradable from mono PERC, and HJT, which requires a different cell process. This transition underscores the need for technological upgrades and increased investment in cell manufacturing capabilities.”
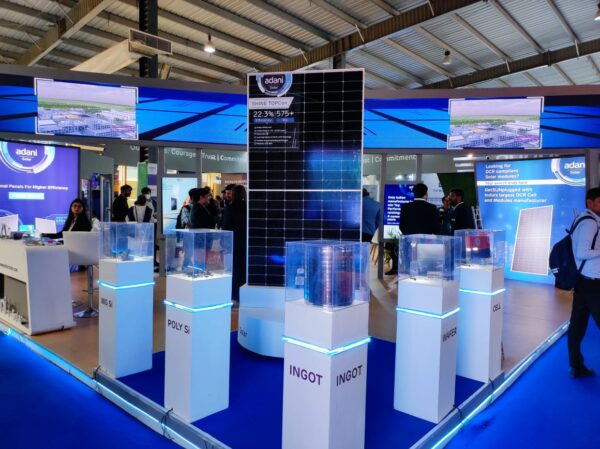
Adani Solar
According to Garg, key challenges to ramping up cell production include high capital expenditure for establishing manufacturing facilities, the necessity of technological advancements, and the recruitment of skilled manpower.
Right now, TOPCon and HJT are the two competing technologies. “HJT technology typically involves more complex manufacturing processes than conventional solar cell technologies like monocrystalline PERC and TOPCon. This complexity can result in higher production costs, making HJT panels more expensive. In markets like India where cost competitiveness is crucial, the higher upfront cost of HJT panels could be a barrier to adoption,” said Tanmoy Duari, CEO, AXITEC Energy India.
DCR cell unavailability: a temporary problem?
The current shortage of DCR cells indeed poses a significant challenge, given an expected increase in the demand from government-supported residential solar projects.
“This year, rooftop solar is trending as the government has approved the PM-Surya Ghar: Muft Bijli Yojana with a total outlay of about $9 billion to install rooftop solar and provide free electricity every month for 10 million households. There is new excitement among solar panel manufacturers to fulfill this demand in the next 18 months,” Amol Anand, co-founder and director of Loom Solar tells pv magazine.
However, DCR cells supply is seen as a transient issue. “The construction of new cell manufacturing plants and the eventual operationalization of capacities under the PLI scheme to mitigate the demand-supply gap. However, these solutions will require time to fully materialize and may initially be insufficient to meet the combined demands of the domestic and export markets,” Garg said.
Policy considerations
Given the crisis in sourcing quality domestic cells and the logical disconnect in their pricing, there’s a strong argument against the continuation of the DCR mandate in its current form.
“The variance in prices among suppliers claiming to use DCR cells, which affects the cost and efficiency of solar projects, further complicates the issue. Instead of a strict DCR mandate, adopting a broader Domestic Content Requirement that encompasses up to 50% of the total Balance of System (BoS) could stimulate the development of ancillary industries like frames and glass, which are crucial to the solar panel sector but not covered under the PLI scheme,” said Garg.
This content is protected by copyright and may not be reused. If you want to cooperate with us and would like to reuse some of our content, please contact: editors@pv-magazine.com.
2 comments
By submitting this form you agree to pv magazine using your data for the purposes of publishing your comment.
Your personal data will only be disclosed or otherwise transmitted to third parties for the purposes of spam filtering or if this is necessary for technical maintenance of the website. Any other transfer to third parties will not take place unless this is justified on the basis of applicable data protection regulations or if pv magazine is legally obliged to do so.
You may revoke this consent at any time with effect for the future, in which case your personal data will be deleted immediately. Otherwise, your data will be deleted if pv magazine has processed your request or the purpose of data storage is fulfilled.
Further information on data privacy can be found in our Data Protection Policy.